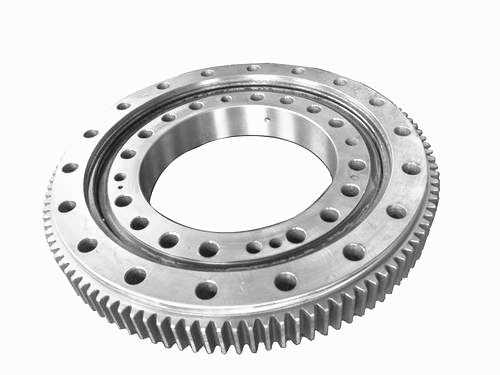
Slewing Bearing
Slewing Bearing could bear the combination load of large axial load, radial load and tilting moment, it is a large bearing with special structure, which has the multi-function of support, rotation, transmission and fixation.
The common used structures of slewing bearing are four-point contact ball slewing bearing, double-row ball slewing bearing, three-row roller slewing bearing and crossed roller slewing bearing, and according to the distribution of gear, slewing bearing mentioned above also could be divided into without gear, with internal gear and with external gear.
FOUR-POINT CONTACT BALL
Four-point contact ball bearings are suited to axial, radial, and moment loads. The four point contact is distributed between the balls and the two split raceways. The precision grinding and geometry of the ball and deep grove raceway allow for the application of increased thrust and moment capacity. Typical applications for these bearings are: Machine Tools, Radar, Medical Equipment and Construction Equipment.
DOUBLE-ROW BALL
The eight point contact bearing design in principal is the same as the four point contact bearing with an additional ball and raceway configuration placed adjacent in the vertical axis’s, this allows for loading to be evenly distributed between the two raceway arrangements, this configuration will allow for an increase in loading capacity of between 75-80% as opposed to the four point contact bearing, with additional dynamic forces being made available of up to 50% (approximately).
THREE ROW ROLLER
These designs provide for the highest load rating of all designs. The three roller configurations allow for the two rollers in the vertical axis to take both axial and moment loads from the two adjacent raceways, whilst the third roller facilitates the radial load. Typical applications for these designs are in Construction, Opencast Mining and Marine applications.
CROSSED ROLLER
The roller and raceway are positioned at 45 degrees to the axis. The static loading capacities for these designs relative to the roller surface contact area are superior as opposed to the four and eight point contact bearings, additionally; the rigidity in this design allows for higher rotational speeds and will allow for a greater degree of misalignment in mounting. However, radial thrust limitations are less than that of the four and eight point contact bearing design. This design is widely used in crane, construction and military product.